Hinges are the foundation of controlled movement in industrial doors and gates.
Door hinges and gate hinges differ in load capacity, materials, and design—making each suitable for specific industrial applications.
Their structural and functional differences directly affect performance, longevity, and safety in manufacturing environments.
Definition and Purpose of Door Hinges vs. Gate Hinges
Door and gate hinges serve the same mechanical function—enabling rotational movement—but are built for different operational settings.
Door hinges are typically used for interior or controlled environments, while gate hinges are designed to support heavier structures, often outdoors.
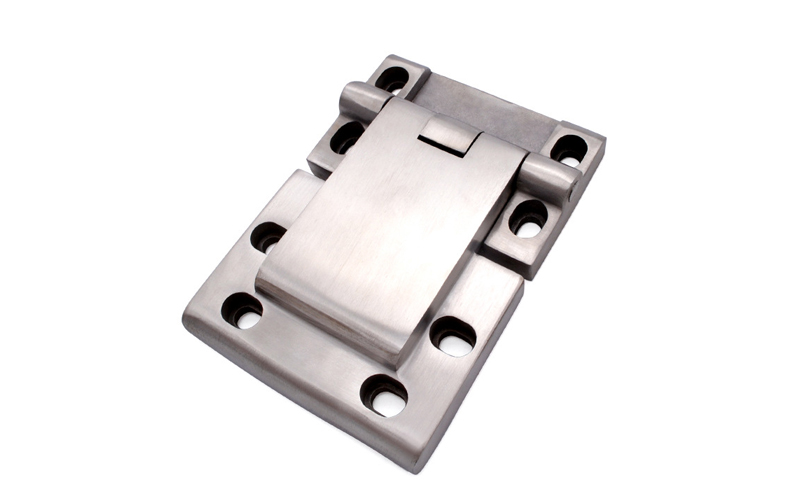
In industrial settings, door hinges are usually lighter, offering ease of installation and smooth movement for panels such as climatic test chamber hinges or cold storage room hinges. These environments demand precise closure and tight sealing over brute strength.
On the other hand, gate hinges are built to support massive swinging structures like access gates to machinery enclosures, trailer compartments, or loading docks. These often endure outdoor exposure and require structural integrity to withstand elements and vibration. Therefore, gate hinges are designed with high durability and reinforced movement mechanisms to prevent misalignment and sagging over time.
Structural Design Differences
The difference begins in their physical structure—gate hinges are more robust and may include enhanced features for stability.
Gate hinges often have extended arms or strap designs to spread the weight over a larger area, reducing structural stress.
Standard door hinges—including butt hinges—feature rectangular leafs and a knuckle formed by interlocking loops, suitable for even distribution on flat vertical surfaces. These are ideal for electrical cabinets or concealed hinges in test chambers, where compact operation is required.
In contrast, gate hinges may come with band and gudgeon configurations or tee hinges, allowing secure mounting on posts or steel frames. These designs are engineered to manage torque and vibration, especially useful on heavy gates like trailer door hinges. The elongated leaf arms not only strengthen attachment but reduce pressure on the central pivot point, increasing the hinge’s operational lifespan.
Load Capacity Considerations
Weight-bearing capability is one of the most crucial distinctions between the two types of hinges.
Gate hinges support loads exceeding 200 lbs, while door hinges typically handle 50–100 lbs in industrial settings.
Industrial gates—such as those on heavy-duty machinery or transport containers—are constructed with thick steel or reinforced aluminum, necessitating heavy duty hinges with exceptional load ratings. Failure in such applications can result in injury or equipment damage, making precise hinge selection critical.
Conversely, door hinges support lighter structures but must provide accurate, smooth motion for repeated opening and closing. Applications like aluminum hinges in test environments benefit from lighter load demands and corrosion-resistant finishes. While door hinges may be rated lower in weight, they often excel in performance under repeated, low-impact motion.
Material Differences
Material choice impacts both strength and resistance to environmental conditions.
Gate hinges are built from galvanized steel or wrought iron for strength, whereas door hinges may use aluminum or stainless steel for corrosion resistance.
Industrial gate hinges are often used in outdoor or semi-exposed areas—requiring coatings or alloys that resist rust, UV damage, and physical deformation. This is why marine hinges are also adapted from gate hinge concepts: both are exposed to harsh climates and corrosive atmospheres.
For example, a cam rise hinge on a heavy gate must lift the gate slightly as it opens, requiring robust metal alloys to sustain repeated use. In contrast, door hinges in test chambers, such as detachable hinges or soft close hinges, prioritize smooth function, modularity, and reduced noise, using high-grade stainless steel or anodized aluminum.
Environmental Adaptability
Industrial hinges must endure very different environments—indoors vs. outdoors, clean vs. harsh.
Gate hinges are designed to resist weather and temperature changes, while door hinges focus on controlled environments and frequent operation.
Gate hinges often support access to outdoor units or shipping docks, where temperature swings, dust, and moisture are unavoidable. These conditions demand weld on hinges or galvanized strap hinges capable of withstanding corrosion and warping.
In contrast, hinges for enclosures, chambers, or server boxes are used in predictable, clean-room conditions. For example, piano hinges in industrial hinge production base environments are ideal for long, even support across an enclosure door—perfect for stability without compromising space efficiency.
Specialized Types of Gate Hinges
The variety of gate hinge types reflects the diverse operational needs in industrial setups.
Gate hinge types include strap hinges, band and gudgeon, tee hinges, and self-closing variants—each suited for a specific gate structure.
Strap hinges provide long-levered support for wide gates, commonly used in shipping crates or factory yard barriers. Self-closing hinges, often spring-loaded, ensure automatic return for security-sensitive areas.
Tee hinges are frequently used on medium-weight industrial access doors where quick installation and broad surface support are needed. These designs reduce stress on mounting points while enabling full swing range. Band and gudgeon hinges, though more traditional, are essential for oversized or vertically heavy gates requiring deep pivot penetration and solid support posts.
Compatibility and Use Cases
Can door hinges be used on gates? Technically yes, but it’s not recommended in industrial settings.
Using a door hinge on a gate compromises safety, lifespan, and alignment—industrial gates need purpose-built gate hinges.
Industrial gate systems often involve significant force during operation—particularly when mechanical openers or security locks are involved. A door hinge in such cases may deform or shear under the stress. Conversely, in certain applications like lightweight panel access doors or modular equipment hatches, heavy-duty gate hinges may be repurposed for added stability.
Knowing when and where each hinge type applies ensures efficiency and safety across operations.
Gate Hinge Sizing and Selection
Choosing the correct hinge size is essential to prevent failure and improve mechanical efficiency.
Gate hinge size charts and specifications guide the selection based on width, weight, swing direction, and mounting surface.
To illustrate, for a 5-foot-wide steel gate weighing 150 lbs, a pair of 12-inch heavy duty strap hinges is recommended. For aluminum industrial cabinets, 4-inch aluminum geared continuous hinges might suffice.
Hinge dimensions, pin diameter, knuckle length, and offset all play roles in selecting the right hinge. Referencing technical datasheets and consulting with engineers (or manufacturers like IHINGES) helps avoid costly rework or structural failure.
Installation Differences
Proper mounting methods differ significantly between hinge types.
Door hinges are recessed into a cutout, while gate hinges are usually surface-mounted or welded for added strength.
In industrial door systems, especially those that use cold storage room hinges, flush installation helps maintain airtight seals. In contrast, gates often use surface-mounted or weld on hinges, especially in environments where tamper resistance or weight distribution is critical.
The difference in installation style also reflects maintenance practices—surface-mounted hinges are easier to replace in the field, a crucial feature for industries prioritizing minimal downtime.
Industrial Applications and Standards
Industry-specific applications demand adherence to stringent mechanical standards and certifications.
Gate hinges are used in transport trailers, machinery enclosures, and field barriers, while door hinges appear in cabinets, test equipment, and indoor enclosures.
Industrial buyers—especially in sheet metal fabrication, test equipment manufacturing, and electrical enclosure production—seek hinges not only by function but by standard compliance. For example, many gate hinges must meet ASTM load test requirements, while door hinges in clean-room or test environments must pass ISO sealing and motion tests.
Manufacturers such as IHINGES provide engineered solutions, including custom logo engraving, 3D design plans, and export-friendly logistics for North America and Southeast Asia.
Conclusion
Gate and door hinges serve distinct industrial functions—selecting the right hinge ensures structural integrity, safety, and operational longevity.