Choosing the right hinge material is critical in industrial manufacturing to ensure performance, safety, and durability in demanding environments.
Stainless steel hinges are generally superior to brass hinges in industrial applications due to their higher strength, better corrosion resistance, and endurance in extreme environments. Brass offers aesthetic value and machinability but lacks the mechanical durability required for high-stress industrial use.
Let’s explore how these two materials perform under real industrial conditions.
What Are Brass and Stainless Steel Hinges Made Of?
Understanding material composition is key to choosing the right hinge for your industrial application.
Brass is a copper-zinc alloy, valued for its ease of machining and attractive appearance. Stainless steel, on the other hand, is an alloy of iron, chromium, and sometimes nickel or molybdenum—designed to resist rust, corrosion, and wear under extreme use conditions.
Hinge Material Composition & Properties
Brass hinges are usually forged or cast and then machined into precise shapes. Their softer nature allows intricate detailing and smoother finishes, often used in light-duty or decorative applications.
Stainless steel hinges are fabricated through stamping, welding, and finishing techniques suited for mass production. This material provides a robust structure, suitable for heavy duty hinges, trailer door hinges, and enclosures exposed to harsh environments.
Property | Brass | Stainless Steel |
---|---|---|
Corrosion Resistance | Moderate (non-acidic) | High (especially 316) |
Strength | Low to Medium | High |
Machinability | Excellent | Moderate |
Magnetic | No | Some grades (yes) |
Cost | Higher | Moderate |
Which Hinge Material Offers Better Corrosion Resistance?
In industrial settings, corrosion can lead to functional failures and safety hazards.
Stainless steel hinges outperform brass in corrosion resistance, especially in wet, saline, or chemical-heavy environments. This makes them ideal for sectors like refrigeration, marine equipment, and chemical processing.
Corrosion Performance in Industrial Environments
Stainless steel (especially grades 304 and 316) is engineered to resist oxidation and corrosion, even in coastal or high-humidity regions. Marine hinges, for instance, are often made from 316 stainless steel due to their enhanced resistance to saltwater.
Brass, while resistant to tarnishing, can experience dezincification in corrosive conditions, leading to structural weaknesses over time. It’s not suitable for outdoor industrial hinges or environments with high chlorine or sulfur content.
Environment | Recommended Material |
---|---|
Coastal/Marine | 316 Stainless Steel |
Dry Indoor Use | Brass or Steel |
Humid/Industrial Kitchen | Stainless Steel |
Cold Room / Refrigeration | Stainless Steel |
How Do Brass and Stainless Steel Hinges Compare in Load Capacity?
Load-bearing strength is vital in industrial applications like large enclosures and equipment doors.
Stainless steel hinges support significantly heavier loads than brass, making them the superior choice for high-stress environments like climatic chambers or machinery housings.
Strength and Structural Integrity
Brass is a soft metal, prone to bending or cracking under continuous heavy loads. It performs well in static, light-load environments but fails in dynamic or high-weight applications.
Stainless steel hinges can bear repetitive mechanical stress without fatigue or deformation. This makes them ideal for use in:
-
Cold storage room hinges
-
Climatic test chamber hinges
-
Industrial access doors
-
Large butt hinges and weld on hinges
Brass simply cannot match this performance level, especially over time.
What Are the Cost Differences Between Brass and Stainless Steel Hinges?
Pricing influences B2B procurement, especially for large-volume hinge sourcing.
Brass hinges are typically more expensive than stainless steel due to the rising cost of copper and the detailed finishing processes involved.
Cost vs. Performance Evaluation
While brass may offer a visually appealing finish and smoother machining, its cost often outweighs its benefits in industrial use cases. Stainless steel hinges, by contrast, are more cost-effective in terms of lifecycle value.
Key cost considerations:
-
Brass: Higher base material cost, higher polish/finish cost, lower strength-to-weight ratio.
-
Stainless Steel: Lower maintenance, higher volume availability, reduced failure rates.
For long-term industrial applications, stainless steel offers better return on investment.
Factor | Brass | Stainless Steel |
---|---|---|
Raw Material Price | High | Moderate |
Maintenance Cost | Higher | Lower |
Replacement Frequency | More Frequent | Less Frequent |
Lifecycle ROI | Lower | Higher |
Which Hinge Material Is Best for Harsh Industrial Environments?
Environments with extreme conditions demand high-performance materials.
Stainless steel is the best choice for extreme heat, humidity, chemicals, or salt exposure, especially when operating in mission-critical industrial infrastructure.
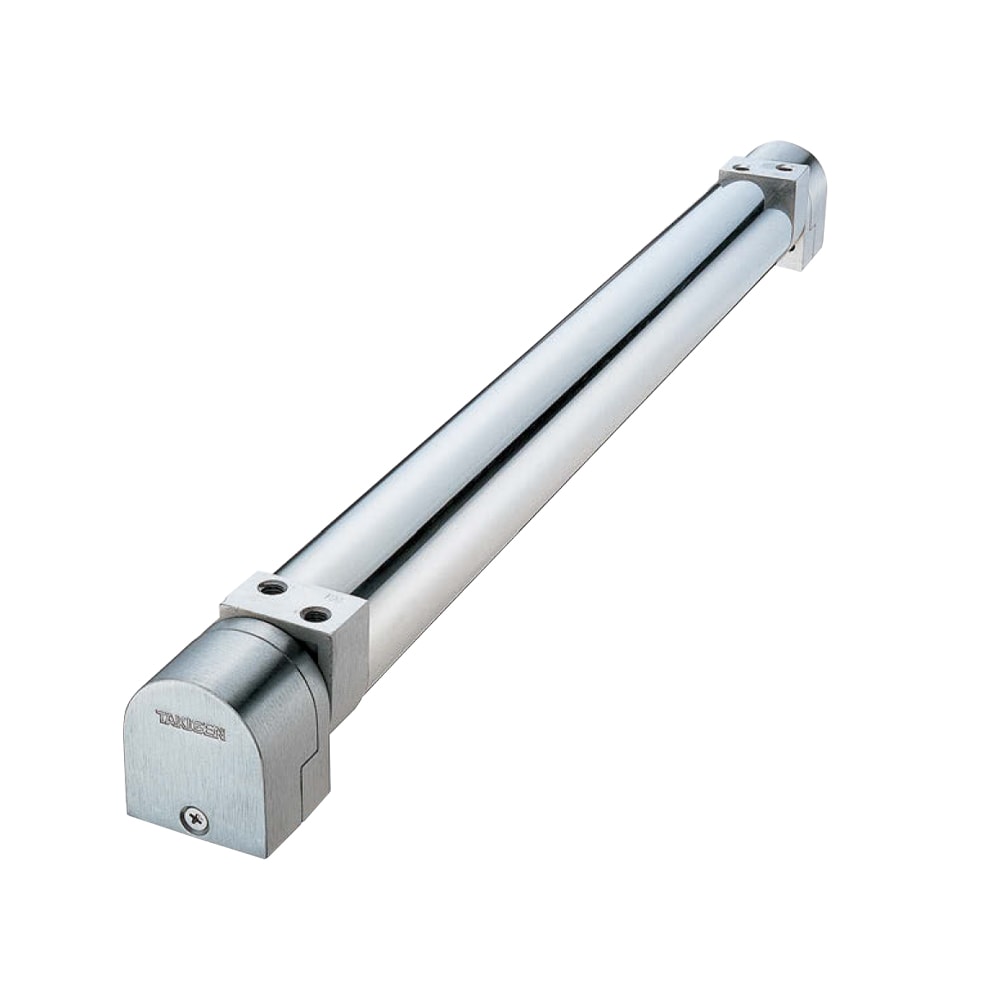
Durability Under Extreme Conditions
Stainless steel hinges are used widely across the industrial sector because they maintain structural integrity across:
-
High/low temperature extremes
-
High humidity or steam
-
Chemical and saline exposures
Brass, while resistant to tarnishing, is not engineered for these extremes. It can weaken when subjected to high thermal stress or corrosive vapors, which limits its suitability for industrial hinge production base applications.
This is why you’ll find stainless steel hinges in:
-
Food processing equipment
-
Marine shipping containers
-
Piano hinges for large panel doors
-
Laboratory or pharmaceutical enclosures
Manufacturing Flexibility: Which Material Is Easier to Work With?
Ease of fabrication can impact lead times and customization in hinge manufacturing.
Brass is easier to machine, but stainless steel is more compatible with advanced fabrication techniques like welding and laser cutting.
Machinability vs. Fabrication Stability
Brass:
-
Easier to drill and tap
-
Ideal for decorative or soft close hinges
-
Better for small batch runs with intricate detailing
Stainless Steel:
-
Higher wear on tools during machining
-
Excellent for detachable hinges, staked hinges, and products requiring welding or structural reinforcement
-
More stable under CNC and laser manufacturing environments
If your production process involves frequent customizations or CNC-driven designs, stainless steel is the more scalable and industrial-grade choice.
Are There Industry Certifications and Standards to Consider?
Certifications ensure safety and compliance in manufacturing.
Stainless steel hinges are more likely to meet stringent industrial certifications for corrosion, load, and fire safety compared to brass.
Compliance Considerations in Industrial Procurement
Stainless steel hinges are widely available with documentation for:
-
ISO 9227 Salt Spray Testing
-
ASTM A240 Material Compliance
-
UL fire rating (where applicable)
-
RoHS and REACH directives for environmental compliance
Brass hinges may be limited to basic corrosion testing and cosmetic finish certifications. For regulated industries, stainless steel is the preferred — often required — material.
Industries like aerospace, marine, and pharmaceuticals often demand documented hinge performance, which brass options can rarely provide.
Conclusion
For industrial use, stainless steel hinges clearly outperform brass hinges in durability, strength, and corrosion resistance—making them the best long-term investment.