The production of industrial products is often a complex process, and today we are going to describe how an industrial hinge is produced and delivered to a customer. I’ve broken it down into roughly six stages as follows.
Confirming the need for the industrial hinge
-
Customers provide samples, and we produce directly according to the samples.
If the customer provides a physical sample, then only the sample needs to be produced as it is. This process may be simpler. But first, we need to review if it is possible to manufacture the customer’s sample. If so we will discuss with the customer some key details of the product that need to be taken care of.
Finally, we will make drawings and produce the product molds. After the molds are produced, we will produce samples and deliver them to the customer to confirm if they meet the customer’s requirements.
-
The customer provides the drawing, produces according to the drawing
If the customer only provides drawings, then we need to simulate the drawings in 3D and confirm them with the customer, and also discuss some key details and whether our production capacity can meet the customer’s requirements. The next step is also to provide samples to the customer for confirmation.
-
Customers put forward the requirements, we come up with the design and drawings, and customers confirm the production
The last case is when the customer can only put forward some requirements and doesn’t know exactly what the structure of the product is, or at least needs to meet those requirements put forward by the customer.
This is the most challenging time for engineers, and this is what IHINGES is best at doing. This is because it gives engineers a lot of room to play. And the engineer can propose solutions that exceed the client’s expectations based on experience and expertise. On the one hand, designers can design very cool products, and on the other hand, they can meet the customer’s requirements. Of course, we need to solve the most basic requirements such as economy and practicality for our clients first.

Confirm the industrial hinge program
Once the engineers have fully understood the customer’s needs, they will draw a 3D mock-up of the product on the computer and give the production department the production drawings of all the parts.
The production department will produce the molds according to the drawings, which may take a little longer, usually around 25-30 days.
After the molds are produced, samples will be produced immediately. The mold will be adjusted according to the sample to achieve the best production condition. The samples will be sent to the customer for confirmation. This process will be done only after the customer has made a certain amount of advance payment.
Confirmation of industrial hinge samples
After the customer receives the sample, we will confirm the sample and if it does not meet the requirements, we will negotiate with the customer to solve the problem and re-produce the sample. However, if the customer makes new requests during the process, things may become more complicated.
Since the production tooling is already produced, adding new changes is a time-consuming and costly task. Generally, this rarely happens.
Of course, requests that are within our tolerance range are possible. We try to meet our customers’ requirements by providing perfect samples
Mass production
After you confirm that the industrial hinge sample is OK, we will proceed to mass production according to the final confirmed sample plan. We will tell our customers the length of this production process in advance. And also communicate with you in time to report the progress of production.
We will also make preparations for the shipment, and confirm with the customer the shipping method, shipping time, and packaging requirements of the product.
During batch production, we will conduct strict quality inspections on each product. Make sure the products received by customers are in good condition.
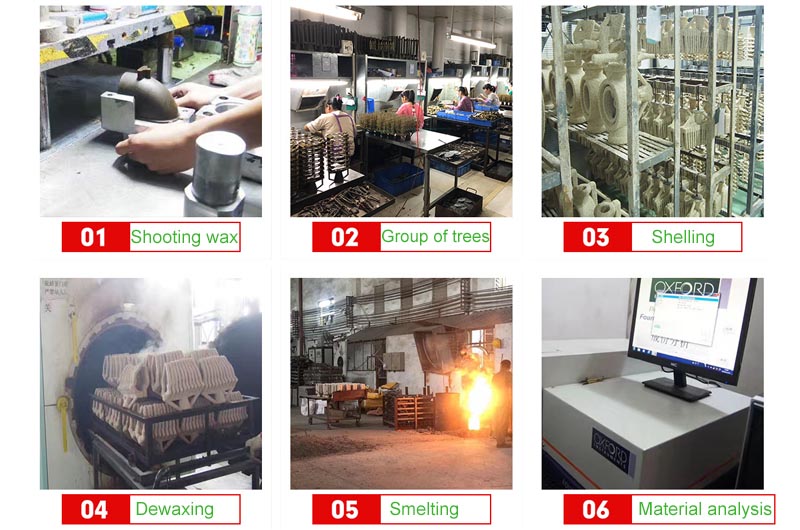
Shipment
We will pack the goods after production. And also mark and explain the products according to the customer’s requirements. We will prepare all the accompanying product documentation.
Generally, we will provide customers with photos or videos of the finished packing by email. Let the customer see what the goods look like before shipping, the heart will feel more at ease. In this process, I will receive the final payment from the customer.
After Sales Service
We will continuously follow up on the arrival of goods, and after-sales issues during the batch use of products by customers. We collect feedback from customers to help improve the production of subsequent products.
After-sales service to customers is actually the beginning of our service, on the one hand, we need to follow up on the customer’s problems in the process of use and solve them.
On the other hand, we need customers to give us some feedback, so that our engineers can verify whether their design is reasonable. Whether it is a reliable design, and summarize the experience to help future product design to do better.